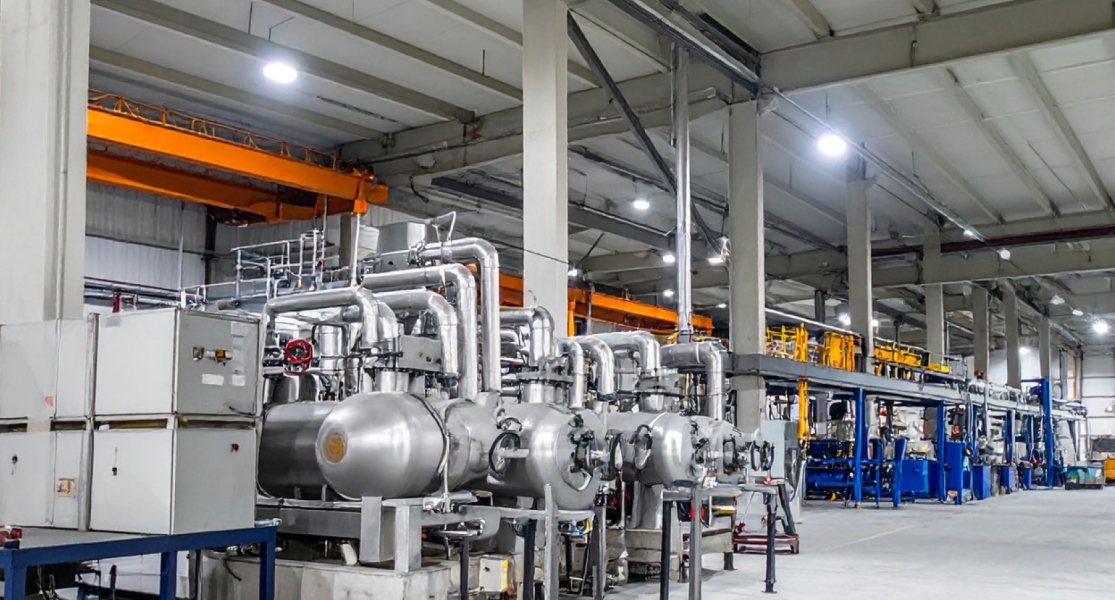
Quadrupling chemical production
Context
Since 2008, ATIS Énergie has been supporting a major chemical producer in its mission to reduce energy consumption at its main site in Quebec. The company’s vast industrial complex is made up of more than 150 buildings.
Our accomplishments
Comprehensive audit of the site performed in 2008
Designed and implemented Engineering, Procurement and Construction Management (EPCM) projects for an integrated energy recovery, management and distribution system in the plant’s most energy-intensive sector
Designed energy recovery systems for distillation columns
Designed and implemented (EPCM) an energy recovery network
Designed and implemented (EPCM) renewable thermal energy production systems
Designed and implemented (EPCM) energy supply and production systems for new buildings on the industrial site
Results
This project, carried out in 2016, involved implementing integrated networks for the recovery, distribution, accumulation and recovery of thermal energy from renewable sources
Deployed a heat network spanning several kilometres
Installed infrastructure to produce renewable thermal energy
Annual reduction in energy consumption equivalent to 9 GWh in electricity and 200,000m³ of natural gas
This producer has expanded its operations in recent years, significantly increasing its production capacity while developing several new products. This growth has resulted in the addition of several dozen new buildings on the site. We were tasked to oversee all industrial processes and energy management for the entire project, to take care of all industrial processes and energy management for the entire project, covering both existing and new buildings.
Our accomplishments
Full site energy audit performed in 2016
Designed and implemented (ECPM) energy-efficient systems for new buildings
Implemented heat recovery systems from exothermic processes, allowing both old and new buildings to be heated, in addition to supplying existing and future exothermic processes
Designed a cooling network for air conditioning new buildings;
Designed and implemented (EPCM) integrated energy systems for all site buildings, both old and new
Designed and implemented (EPCM) several dozen kilometres of heating and air conditioning networks
Results
Our energy management strategy, focused on efficiency and innovation, proved to be cost-effective for our client
We implemented an additional power block of less than 5 MW significantly less than conventional demand requiring close to 30 MW
Energy savings of up to 50 GWh per year, representing a reduction in operating costs of more than $8 million annually
Efficient energy use meant we could avoid using natural gas, thus avoiding the equivalent of up to 9,000 of CO₂ emissions per year
Implemented several tens of kilometres of thermal and air conditioning networks
Deployed exothermic process energy recovery infrastructures, allowing this energy to be redistributed to new and existing heat-consuming buildings and processes
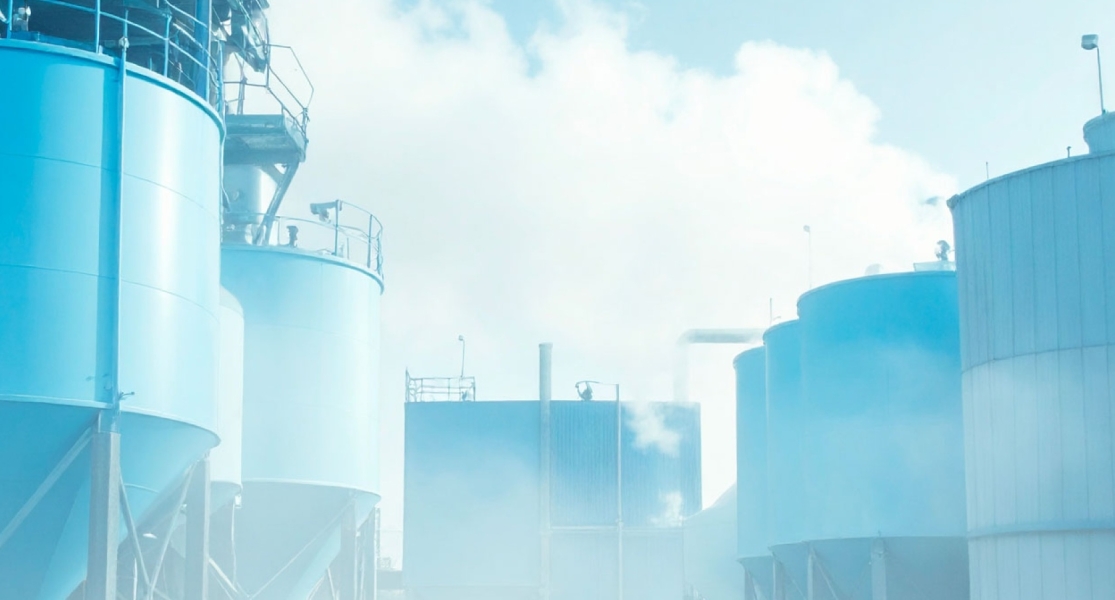
32% reduction in steam production at a pulp & paper mill
Context
Concerned about its energy performance, a pulp & paper mill called on our expertise to identify savings opportunities to bolster its in-house efforts.
Over the years, ATIS Énergie has carried out various opportunity studies at different plants within the company. Each one has revealed significant potential for reducing energy consumption along with greenhouse gas emissions.
One of the studies, carried out at a containerboard plant, showed particularly promising potential. We proposed a solution that involves rethinking the plant’s energy infrastructure to reduce the use of steam by replacing it with hot water, where possible. This approach allows for a more efficient use of thermal energy.
This project will allow the plant to increase its production capacity while maintaining its existing steam production and distribution infrastructure, leading to long-term energy efficiency gains.
Main actions to be implemented
- Reduce steam production in boilers with a series of targeted measures
- Recover heat from evaporator condensers and water tower
- Construction of new facilities to accommodate the majority of equipment required, due to lack of space in existing plant
- Improve the paper machine’s operational flexibility
- Optimize steam shower feed
Expected results
Reduction of 48,000 lb/h (32%) in steam production at the pulp & paper mill, generating annual savings of close to $6 million
Possibility of operating solely on biomass for steam production, with the electric boiler as a backup in the event of a wood-fired boiler breakdown
Both oil-fired boilers can be shut down, eliminating fuel oil consumption
Reduce GHG emissions by 12,000 tCO2e
Annual steam production savings of $7.5 million, resulting in a return on investment in less than 3 years
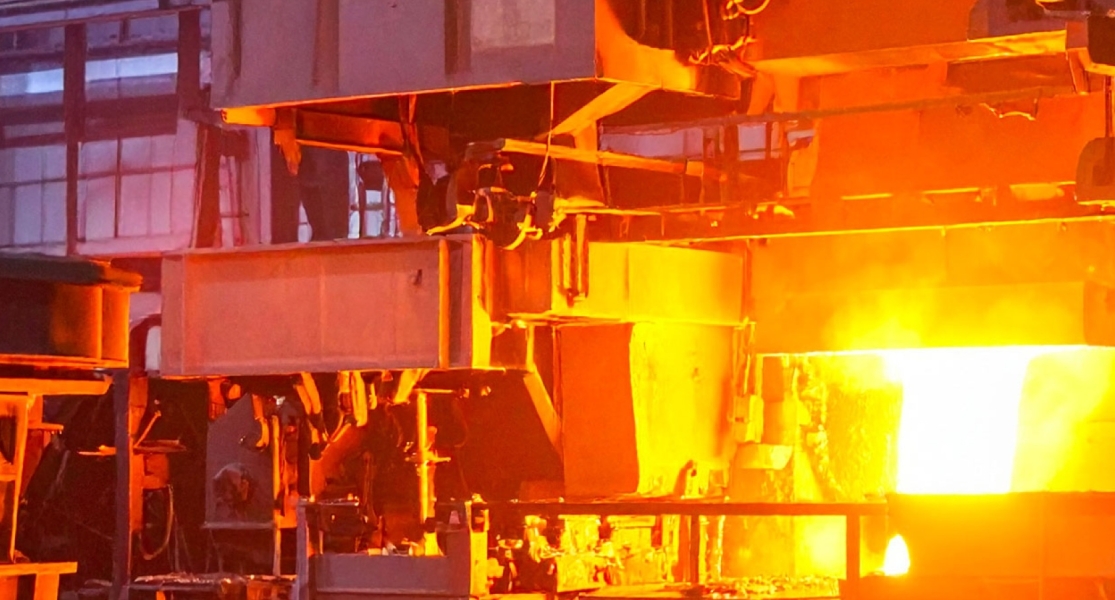
Recovering excess heat from a 50 MW foundry furnace
Context
A foundry identified a high-potential opportunity to generate new revenue by recovering excess heat from its 50 MW industrial furnace. This project involves recovering the furnace’s cooling water at approximately 65°C and converting this heat into superheated steam at a minimum pressure of 12 barg (Tsat 192°C). The goal is to supply the thermal processes at an adjacent plant via a steam network spanning several kilometres.
Our accomplishments
Increase cooling water temperature to 62–65°C and extract heat efficiently
Generate vacuum steam followed by mechanical recompression to 9 barg
Use motive steam from the existing boiler to increase steam pressure to 13–14 barg
Install a 12-inch steam line on the existing route connecting the two plants
Expected results
Approx. 21,000 kg/h of steam produced from the recovery of heat from the cooling water of the furnace
Nearly 5 MW of power used for this production through mechanical recompression
Supply of an additional 15 MW of heat to the client’s plant
Reduction in greenhouse gas emissions estimated up to 25 000 tCO₂e per year
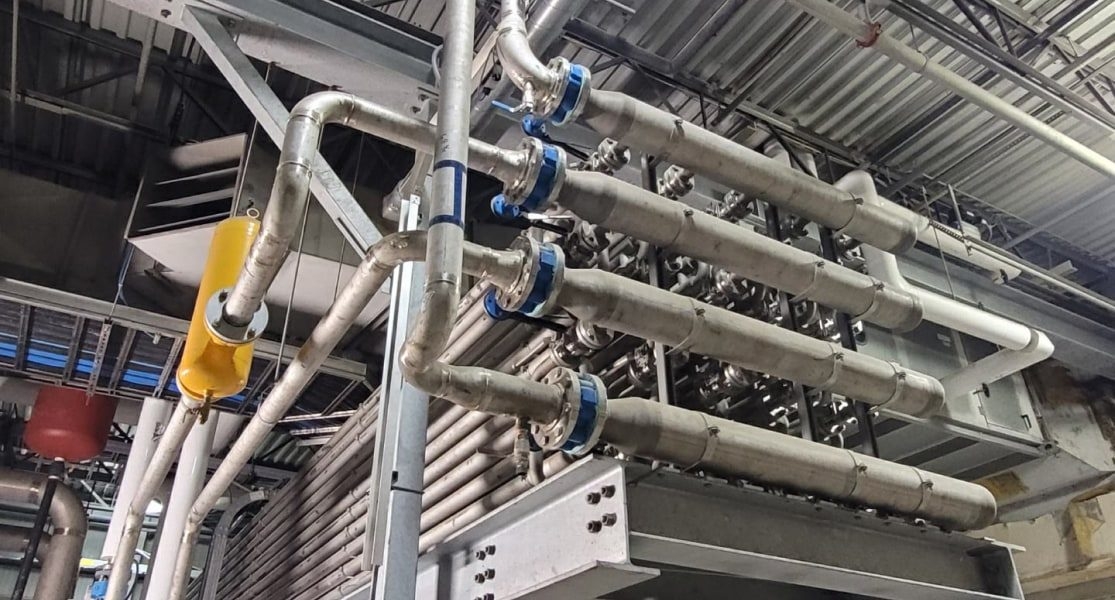
Les Viandes duBreton, Rivière-du-Loup
Context
In an effort to significantly reduce its energy consumption and carbon footprint, duBreton retained ATIS to propose and implement important measures that would help the company achieve its objectives.
The first phase, carried out in 2012, consisted of installing a renewable thermal energy production system using high-temperature heat pumps, amongst other things. The project was largely fuelled by waste heat from cooling systems that recover up to 5 MW of thermal energy. High-temperature heat pumps produce more than 2 MW of energy at > 80°C. The project has completely eliminated fuel oil consumption (more than 1 million litres per year).
The second phase, completed in 2015, significantly reduced the consumption of propane for heating fresh air. Atis Énergie is currently implementing the third phase (2023) of this ambitious energy transition program, which will reduce electrical energy consumption by more than 5 MWh/year in addition to minimizing the use of propane.
Our accomplishments
- Energy audit
- Design and supply of projects for the upgrading, production and distribution of renewable thermal energy for hot water production, fresh air heating systems and dehumidification, including:
- Design and integration of energy recovery systems for cold generation [alt: production] compressors
- Design and supply of effluent energy recovery systems
- Design, supply and installation of a pig hair burner waste heat recovery system.
- Design, supply and installation of an energy management system for an hydraulics system equipped with waste heat recovery system,
- Design and supply of high temperature (3 MW) heat pumps
- Design, supply and installation of fresh air heating system (120,000 CFM)
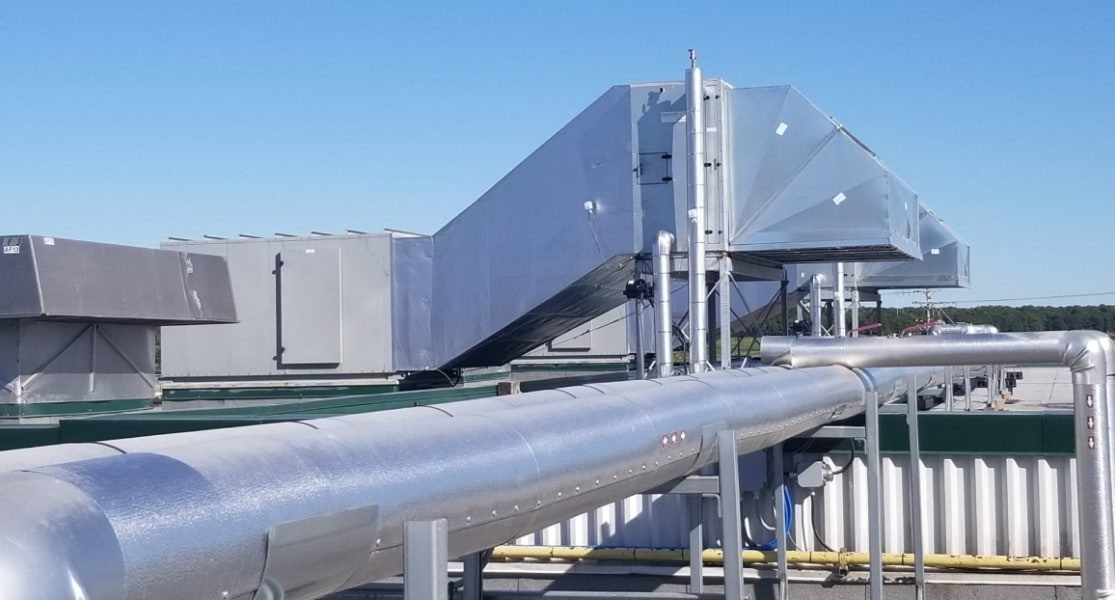
Olymel
Context
With more than thirty processing plants, Olymel is the largest meat producer and processor in Canada. The company wanted to improve their energy productivity. Olymel called on the expertise of ATIS Énergie to improve its environmental performance while reducing its energy consumption and GHG emissions. Atis Énergie has been supporting Olymel since 2017, and to-date has carried out projects in 4 plants: Saint-Esprit, Yamachiche, Vallée-Jonction and Sainte-Rosalie.
Our Accomplishments
Turkey projects:
- Design, supply and installation of a thermal energy recovery system for cooling systems condensers (10-15 MW per plant)
- Design, supply and installation of a thermal energy recovery system for plant effluents
- Design, supply and installation of a renewable thermal energy production system using a 2 MW heat pump
- Design and supply of high-quality thermal energy recovery systems for pig hair burners
- Design, supply and installation of a system for the production and distribution through heat distribution network of thermal energy, as well as a domestic hot water production system
- Design, supply and installation of a thermal energy production and heat distribution network system for a fresh air supply system (80,000-120,000 CFM per plant)
- Design and implementation of an Energy Management Information System (EMIS) for collecting and archiving operational data on energy production by process and production unit
Results
- Up to 80% reduction in GHG emissions
- Over 30% reduction in total energy consumption
- Increased capacity of the condensing systems of the plant's main coolers
- Implementation of thermal energy recovery and production networks with sufficient capacity to satisfy present and future energy requirements
- Design and installation of energy recovery systems for pig hair burners and effluents integrated into the heat distribution network
- Design and installation of energy distribution network to supply energy to fresh air units (80,000 CFM to 120,000 CFM)
- Design and implementation of systems for the production and storage of renewable thermal energy from energy recovery
- Thermal energy consumption and production monitoring system to monitor and detect specific energy trends and deviations

International dairy processing company
Context
A high-profile international agri-food company committed to significantly improving the energy efficiency of its production sites and reducing its greenhouse gas emissions by 2030.
We worked with them to develop a project aligned with their vision—and went even further. The results far exceeded the company’s targets and became its global benchmark for energy savings.
Our accomplishments
In-depth analysis of energy saving potential
Full project management using an ECPM (Engineering, Procurement, Management and Construction) approach;
Gathering required certifications
Identifying and obtaining available subsidies
Implementation of an Energy Management System (EnMS), an Energy Management Information System (EMIS), and support toward ISO 50001 certification
The results
Reduction of more than 5.000 tonnes of GHG emissions per year, representing a significant proportion of total emissions in 2023
More than 30% reduction in energy consumption in 2024 compared to 2023, generating annual savings of over $1 million
ISO 50001 certification - the global standard for energy performance recognition
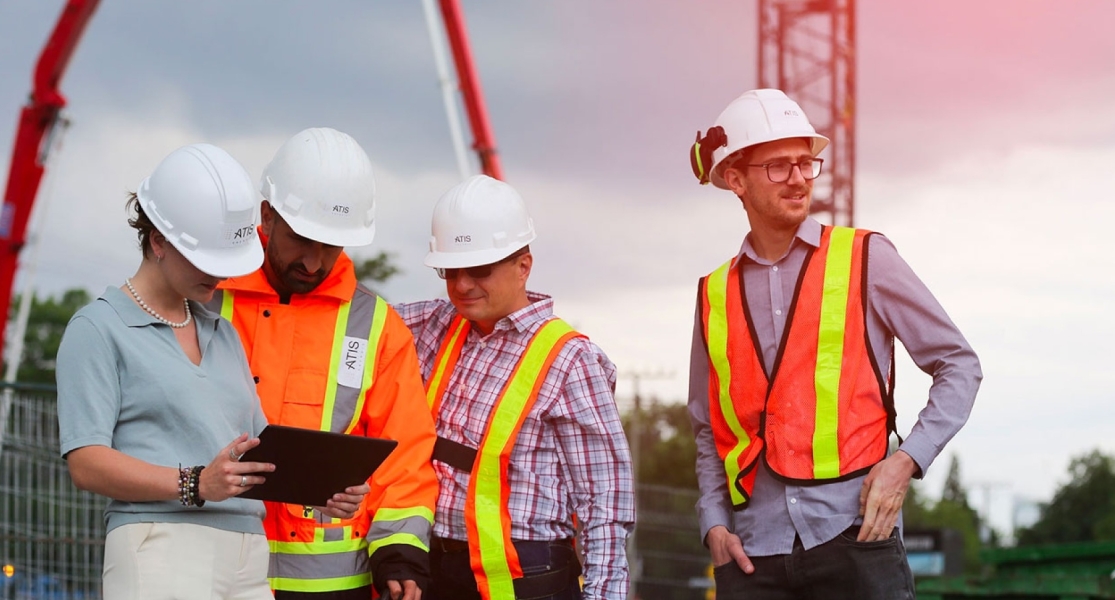
Development of neighbourhood heat networks
Context
From thermal loops to industrial and urban heat networks, we designed and deployed dozens of kilometres of networks, helping reduce energy consumption and greenhouse gas emissions.
In collaboration with Écohabitation, École Polytechnique de Montréal and several municipal and institutional players, our team carried out various opportunity studies to develop the heat networks. Some of the neighbourhoods to benefit from these networks across Montreal include:
Faubourgs;
Écoquartier Louvain Est (Ahuntsic-Cartierville);
Écoquartier Namur (Côte-des-Neiges)
Varennes industrial park
Our accomplishments
Full implementation of the production cycle: engineering, procurement, construction management and commissioning;
Evaluating the need for heat network based on urban resilience and carbon neutrality criteria;
Identifying available energy sources and the most suitable technologies;
Annual energy balance, including heating, cooling and waste requirements;
Analysis of the benefits and limitations of a collective heat network;
Developing an optimal governance model to ensure the success and sustainability of the network.
The results
Created heat and cold loops in factories to recover and/or redistribute energy;
Energy sharing between several buildings on the same industrial site;
Energy transfer between a producer and external client;
Reduced overall energy consumption;
Targeting carbon neutrality;
Helped strengthen urban resilience against climate change.
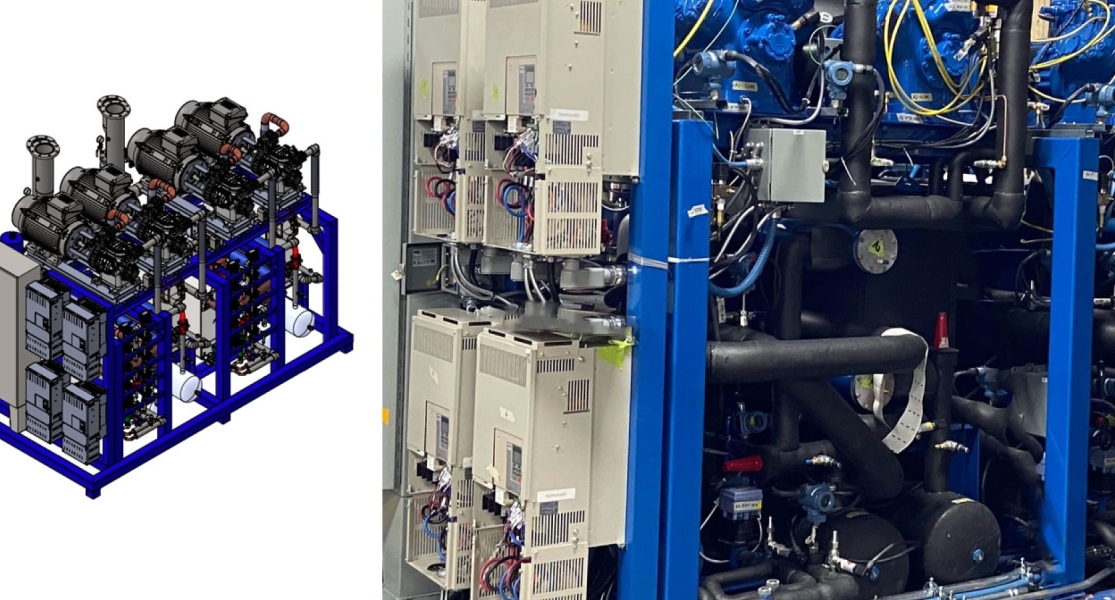
High-temperature industrial heat pumps (hot water)
Context
Our clients were constantly needing to have their heat pumps repaired. To solve the issue, we decided to design and manufacture our own.
Our accomplishments
AT-150 heat pump: 50 kW compressor capacity and 150 kW thermal capacity;
AT-300 heat pump: 100 kW compressor capacity and 300 kW thermal capacity;
AT-600 heat pump: 200 kW compressor capacity and 600 kW thermal capacity;
AT-900 heat pump: 300 kW compressor capacity and 900 kW thermal capacity.
AT-1800 heat pump: 600 kW compressor capacity and 1,800 kW thermal capacity.
Results
Tailor-made solutions combining performance, reliability and durability;
Pushed technological limits to better achieve specific project goals;
Equipment perfectly adapted to operational needs and real-world conditions.
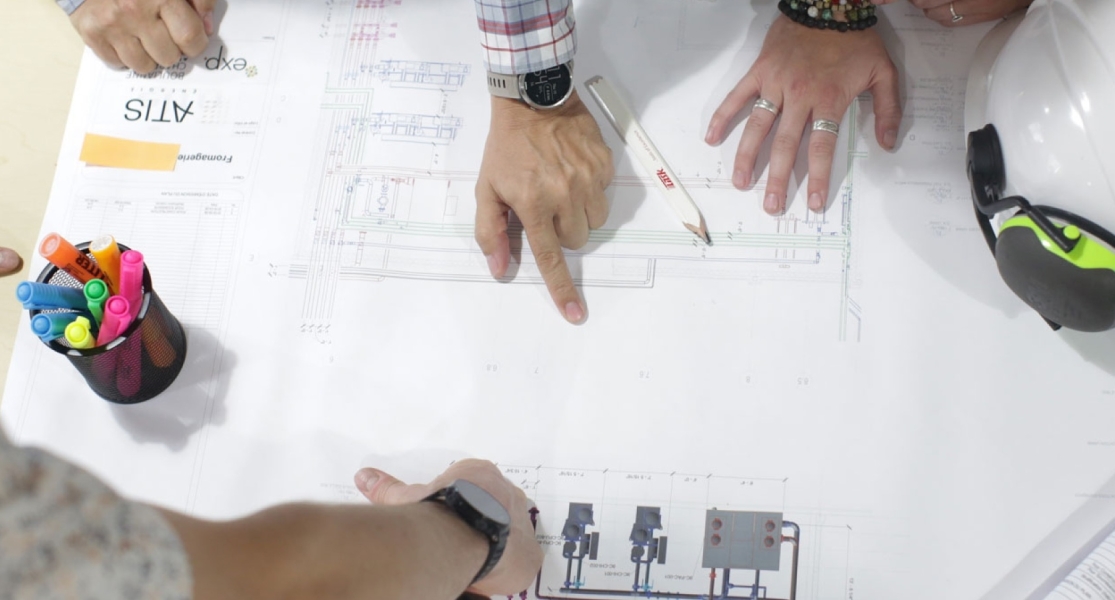
Other custom innovations
Whenever a client approaches us with a complex issue that has no pre-existing solution, or anytime a tech opportunity emerges on the market, we mobilize our team to find original, efficient and sustainable solutions.Just one example: we custom-designed a hair burner to meet the unique needs of our client, Olymel.
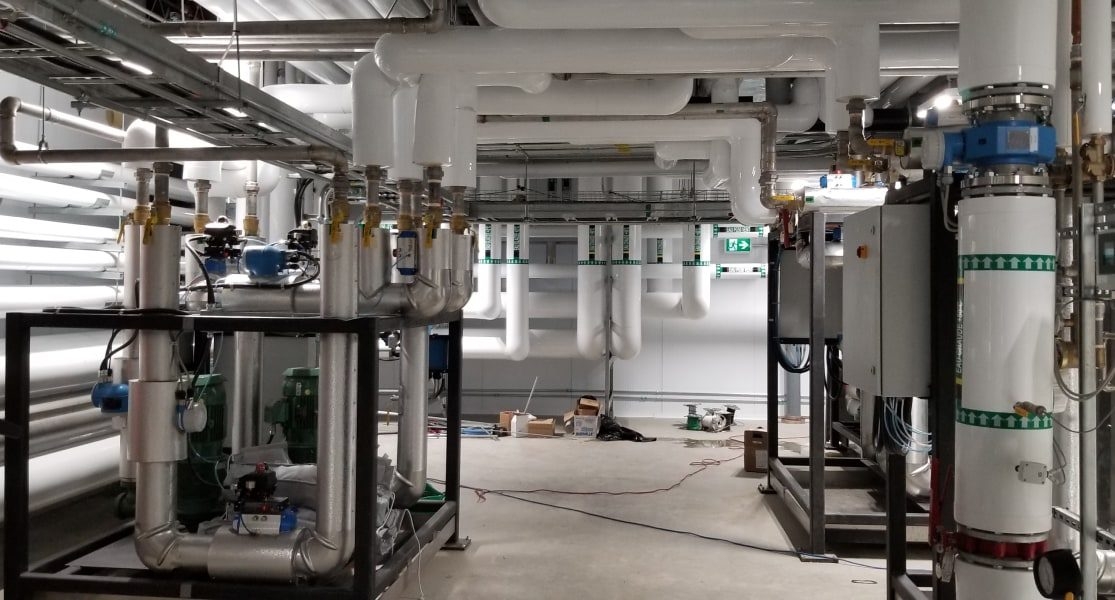
Le Groupe Bel
Context
For the construction of its new cheese production plant in Quebec, Bel Group called on ATIS Énergie to design and implement an innovative thermal energy production system based on resource sharing between 2 plants. The mandate: a concept for the implementation of the plant’s building mechanics and for the integration of a system for the management and production of thermal energy between 2 plants.
Our accomplishments
Energy Audit (2017)
Detailed engineering for building and process mechanics for the construction of the first Babybel production plant in Canada
Project for the design and supply of the modular system for the production and distribution of thermal energy
Design and programming of the control system for the production and monitoring of the plant's thermal energy production
Design, supply and programming of a dynamic ventilation control system to ensure air pressure conditions are maintained between production rooms, according to different production modes
Energy audit of a Bel plant in Portugal
Installation of systems for the recovery of cold and milk, and for preheating pasteurization
85 to 90% reduction in GHG emissions, i.e., more than 1,500 tons of CO2 equivalent
Reduction of the heating and cooling production capacity required by the shared services between two plants (Bel and Riviera)
Real-time automatic balancing of ventilation airflows to maintain relative pressures between different production rooms
Heating of ventilation systems (production and offices), more than 95% of the time with direct heat recovery from refrigeration systems and production processes
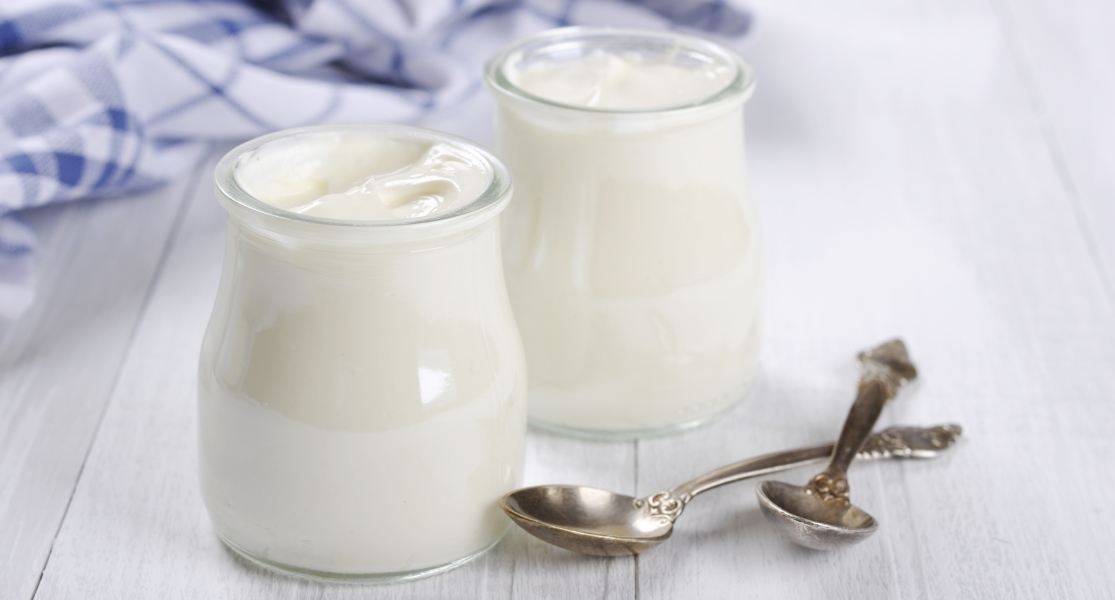
Maison Riviera
Context
In 2013, rapidly expanding company La Laiterie Chalifoux (now La Maison Riviera) wanted to review its energy production and management methods. Atis Énergie assisted them with the setup of the services required for these new operations. The project was carried out in 3 phases between 2014 and 2016.
Our accomplishments
- Design and supply of a centralized refrigeration [alt: cooling] system (phase 1) and a chilled water loop
- Design, supply and installation of a milk cooling recovery system and a milk preheating system (phase 2)
- Installation of effluent energy recovery systems and an energy storage system
- Design, supply and installation of a ventilation system powered by energy from waste (phase 2)
- Design and supply of a thermal energy production system using a high temperature heat pump (phase 3)
Results
- 80% reduction in GHG emissions
- Replacement of the silo refrigeration system (600 tons in total) by a centralized system (200 tons) including a cooling distribution network
- Installation of thermal batteries
- Implementation of a renewable thermal energy production system
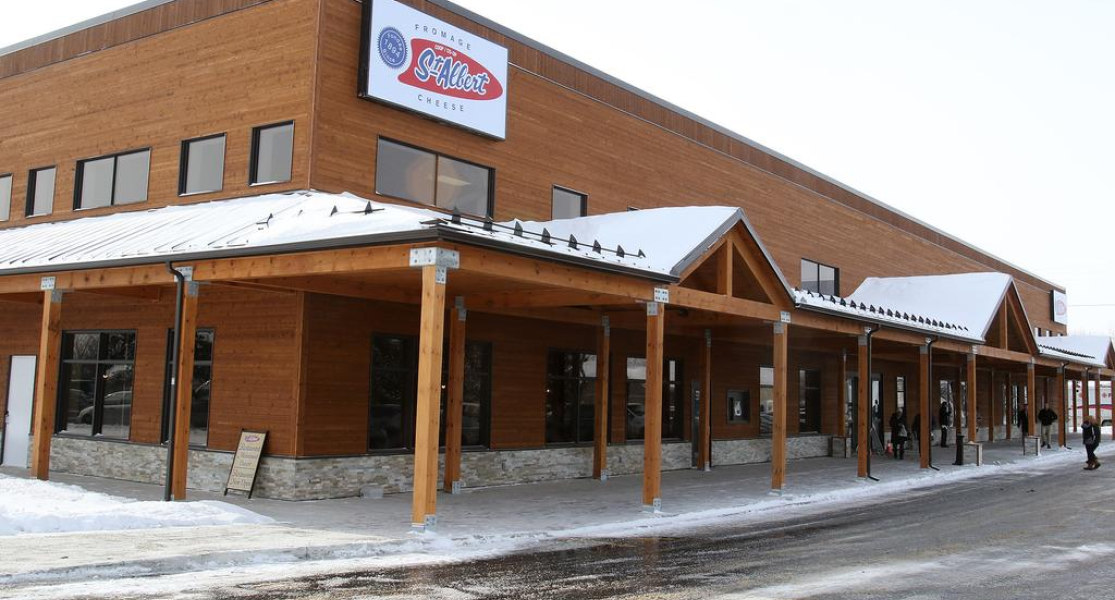
Fromagerie St-Albert, Saint-Albert, Ontario
Context
The St-Albert cheese factory has been in operation since 1894 and today has more than 100 employees. In 2013, the factory was completely destroyed by fire. With its reconstruction, the company got a fresh start (2015). The factory then adopted new methods for steady growth, while limiting the environmental impact of its production. Atis Énergie received the design mandate for all of the building's mechanics, including energy services for the cheese factory, store, restaurant and offices (energy production, hot water, refrigeration and ventilation).
Our accomplishments
- Engineering and deployment of all energy and mechanical systems for the building, including a heating, glycol and chilled water loop
- Provision of equipment: process cooling and heating system, including networks and ventilation for the factory, offices and restaurant
- Design and supply of the control system for the building mechanics
Results
- Systems for the recovery of cold and milk, and for preheating pasteurization
- Cold, milk and pasteurization preheating recovery systems;
- New heating and cooling networks to meet the company’s present and future energy needs
- Condensation energy recovery loop (100%) of the refrigeration system
- Reduction of GHG emissions by more than 60% compared to a typical plant
- Optimized energy costs
- Individually controlled office heating and cooling system (per office, hot or cold) powered by energy from the plant infrastructure
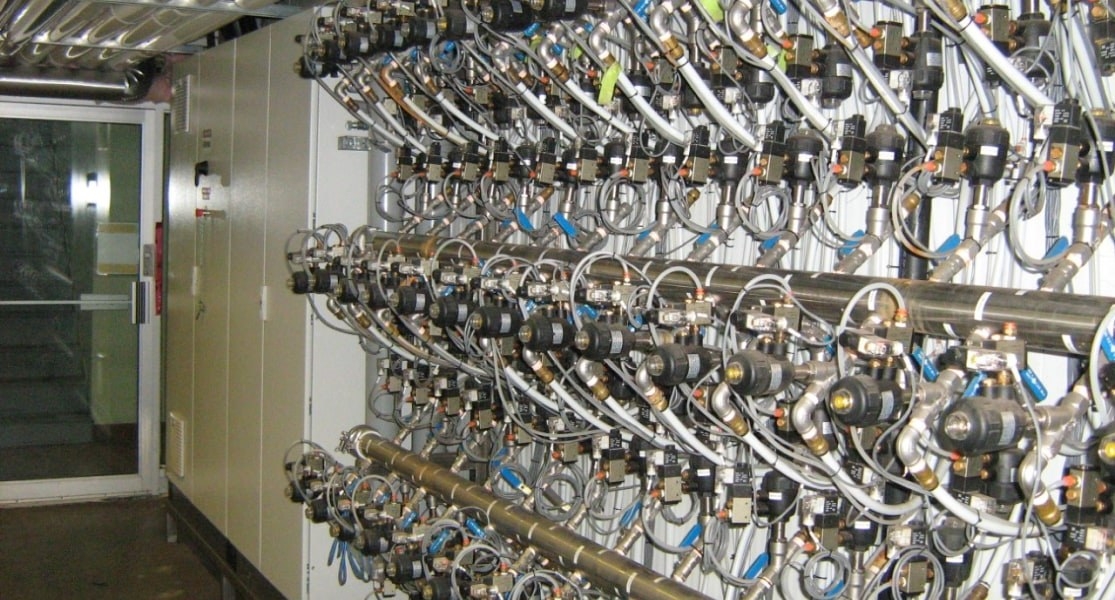
Nutrinor, Alma
Context
With a focus on sustainable development, the agri-food cooperative Nutrinor took measures to reduce its carbon footprint and energy costs. Based on the results of an audit conducted in 2011, Atis Énergie proposed a list of projects and undertook the design of energy production and management systems that meet Nutrinor's objectives and ambitions. These projects were carried out between 2013 and 2017.
Our Accomplishments
- Design and supply of a new, 100% fresh-air plant ventilation system
- Design and supply of a "medium temperature" heat recovery network powered by energy from the chiller’s condensers
- Installation of a heating and cooling system for the offices powered by energy from the heat recovery system
- Design and installation of a high-temperature energy production and management system
- Design, supply and integration of an energy storage system
Results
- More than 80% reduction of GHG emissions and thermal energy consumption
- 15% reduction in electrical energy consumption
- Improved air quality
- Increase in installed heat production capacity
- Increased availability of cold via process improvements
- Installation of the first high temperature heat pump (2014)
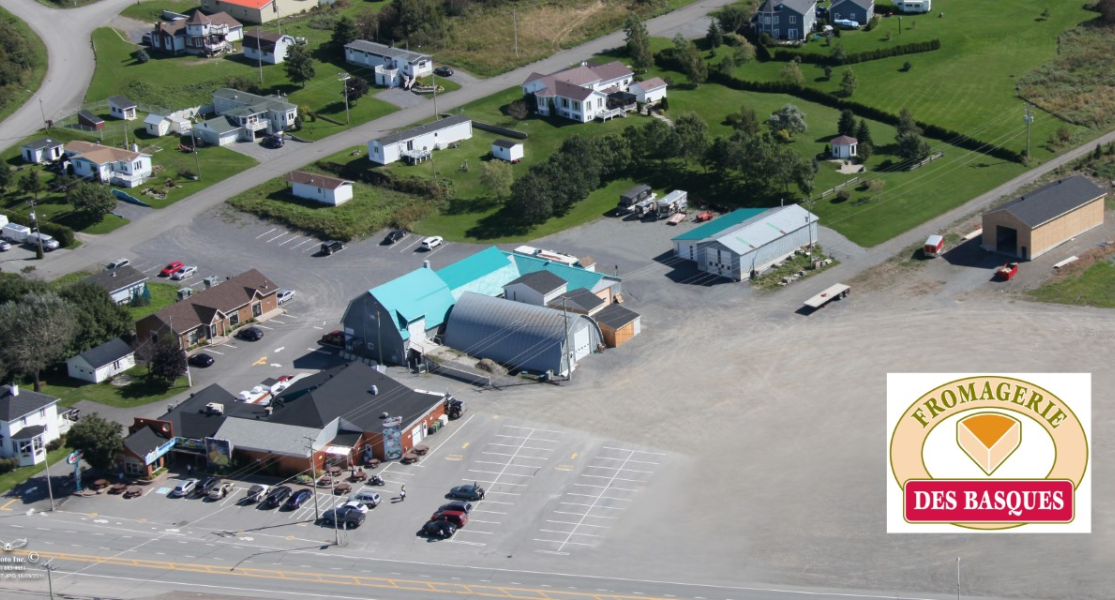
La Fromagerie des Basques
Context
To achieve its goal of developing operational autonomy both in terms of waste management and the production of thermal energy, Fromagerie des Basques turned to Atis Énergie in 2011 to carry out a project for the production, management and recovery of energy resulting from the implementation of a whey biomethanation system.
Our accomplishments
- Design and supply of a biogas energy recovery system (anaerobic digester)
- Design and implementation of a thermal energy production and management system
- Design, supply and installation of a cooling system providing cold to cheese process the fridges and ripening rooms
- Design and installation of a fresh air supply system
- Design and installation of ripening rooms
- Installation of a heat loop network to supply heating and cooling to the cheese plant and three adjoining buildings
Results
- Awarded a first world prize from ASHRAE in 2014 for the biomethanation project and the energy savings
- Installation of a thermal network for cheese production and to supply four buildings
- 70% reduction in GHG emissions
- Operational autonomy for waste management
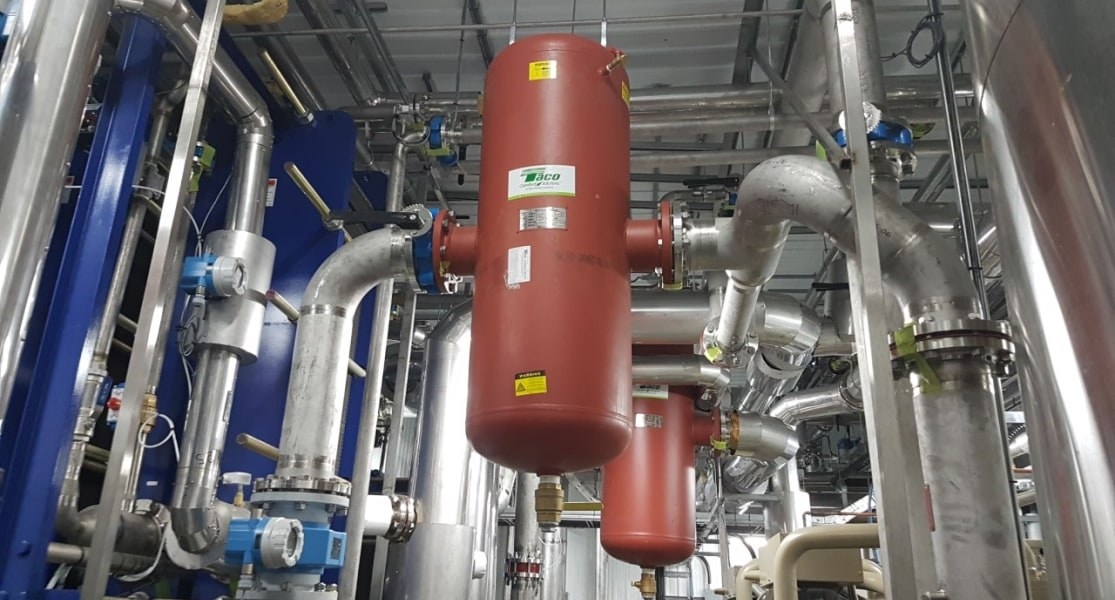
Fromagerie Perron
Context
Fromagerie Perron wanted to minimize its energy consumption while improving its productivity. Atis Énergie supported the cheese producer in achieving this ambitious goal.
Our Accomplishments
- Design and supply of a whey cooling system
- Design and supply of the hot water production system for the Clean-In-Place (CIP) system used to clean process equipment
- Design and supply of the renewable thermal energy management and production system, including high temperature heat pump
- Design, supply and installation of recovery networks, thermal energy production (hot and cold) and networks to supply customers in 2 separate plants
Results
- More than 60% reduction in GHG emissions
- New infrastructure
- Renewable heat production
- Cold production
- Heating and cooling distribution recovery network in its plant
- Network to recover and distribute common heating and cooling to another plant
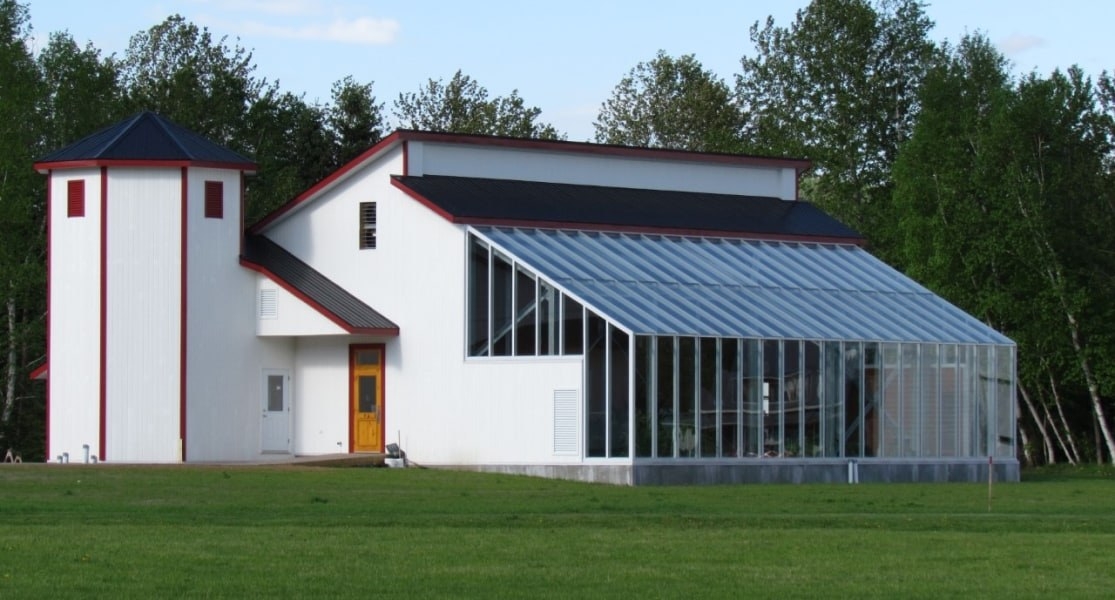
Laiterie Charlevoix
Context
Laiterie Charlevoix wanted to develop its operational autonomy both in terms of managing its residual materials (whey and white water) and its energy. It turned to Atis Énergie to carry out a project for the production, management and recovery of energy from residual materials through the implementation of anaerobic digestion and energy management systems.
Our Accomplishments
- Implementation of a biogas energy production system (methanation)
- Integration of a plant-based post-treatment system (phytology)
- Design and implementation of a thermal energy production and management system for heat production
- Installation of heat loops to supply energy to the cheese plant and an adjoining building
- Design and installation of ripening rooms
Results
- 60% reduction in GHG emissions
- Operational autonomy for managing residual materials
- Installation of a thermal network supplying three buildings
The project won first prize in the Renewable Energy and Energy Efficiency category at the 2012 AQME Énergia gala, and in fact claimed first prize in every category at the gala.
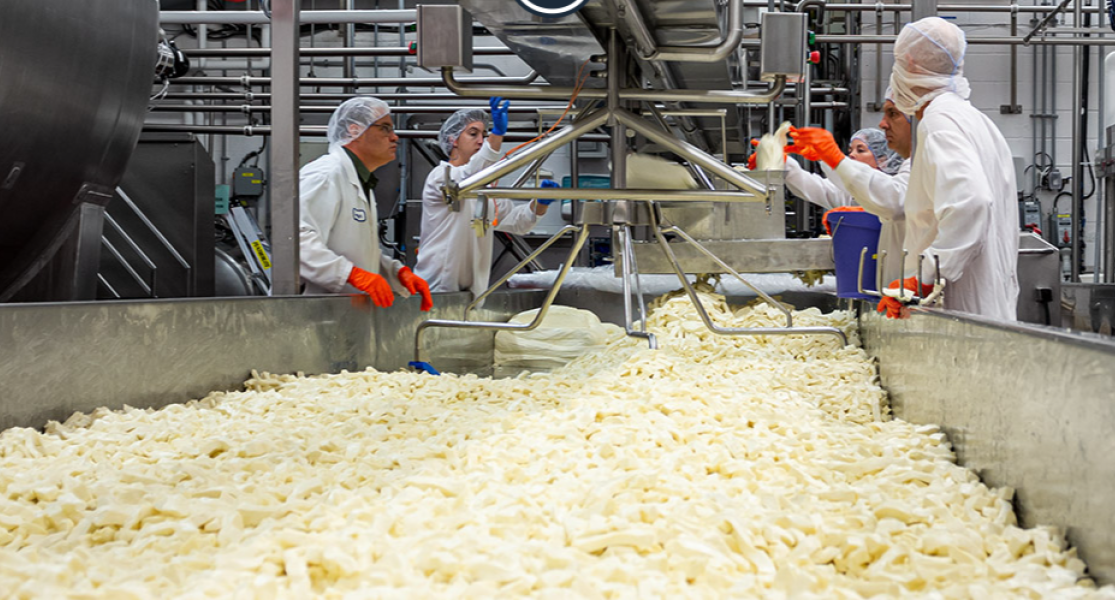
Coop Agrilait, Fromagerie St-Guillaume
Context
Fromagerie St-Guillaume, Atis Énergie’s first “cheese” client, wanted to integrate new energy services into the plant’s mechanics during a plant expansion that included the addition of new administrative offices. The cheese producer has made important changes in its energy management, resulting in significant energy savings.
Our Accomplishments
- Implementation of projects to reduce the energy consumption of the whey drying system by more than 60%
- Improved energy efficiency of 2-effect evaporator and whey drying system
- Design and supply of ventilation system for new administrative buildings and plant
- Energy recovery and management (including a centralized cooling system)
- Design and supply of ripening rooms
- Increased capacity of the plant’s cooling system
Results
- Increased drying capacity of whey drying system
- More than 65% reduction in GHG emissions
- Transformation of fridge operation for glycol operation
- Use of heat pump for independent controlled environment control by administrative office area
- Implementation of significantly more efficient milk pasteurizers
- Installation of thermal batteries